Annual Maintenance Checklist
The MassLandlords annual maintenance checklist is a best practice developed by seasoned property management companies. The annual maintenance checklist will take approximately 17 minutes to complete in a unit with renter cooperation and few defects. Depending on the difficulty with which doors and windows open, the time needed for water to heat up, the number of defects, or the general state of renter possessions, the inspection could take longer. If you are being thorough, the inspection will not take less time. Yes, really do open every cabinet, start appliances, etc.
(This annual maintenance checklist must be followed by owners and managers with the Certified Massachusetts Landlord(TM) designation. Renters and others may submit a report on suspected noncompliance by viewing the owner's professional profile and using the "Report" feature there.)
The annual maintenance checklist does not guarantee compliance with the state sanitary code, which is many times longer and more complicated. But this checklist is a good start, and based on long experience, will capture 90% of what an inspector is likely to cite. It will also capture virtually all long-term maintenance concerns. An ounce of prevention is worth a pound of cure! And it's better that whatever is going to break should do so in your hand than a renter's.
Revisions
- v6
- Internal updates
- v5
- Sign on building -Owner/property manager phone is located in the common area of the building?
- Sink and faucet -Waterproof seal behind the kitchen sink?
- Hood Vent -Is it clean?
- Closet -Is there enough light?
- Heat- Filters Clean? Remote works? leaking, valves in good condition? Vent covers missing/damaged?
- Basement- Chimney in use clean it out?
- Washing machine/dryer- If not in use is the draining pipe capped?
- Common lights - Motion sensors working?
- v4
- Added reminders of deleading compliance
- v3
- Starting version
To view this form, you must be logged-in and a member in good standing
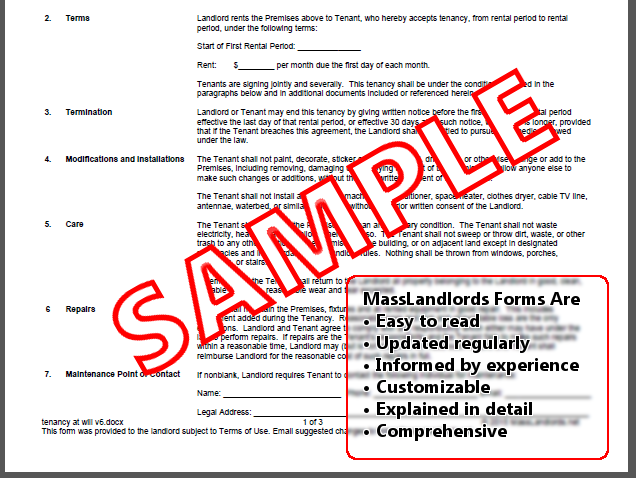
MassLandlords is a nonprofit dedicated to helping owners rent their property. We try our best, but we can't guarantee these forms will always work. We provide legal information but never advice particular to your situation. Nothing on this site is meant to create an attorney-client relationship. We advise you consult with an attorney.