If You Need to Upgrade to 400-Amp Electric Service, Plan One Year in Advance or More
Posted in News - 0 Comments
.By Eric Weld, MassLandlords, Inc.
If you’re planning or need an upgrade of electric service for your home or rentals in 2024, be sure to build in a year or more of delay in obtaining electronic components.
Since 2020, when the Covid pandemic interrupted supply chains globally, orders for electronic components have taken from eight months to more than a year to fill. Items such as semiconductors, circuit boards, electric subpanels and breakers, and smaller parts like switches and transformers continue to be in short supply and slow to arrive.
Compounding the delay is an uptick in demand as consumers continue to convert their homes’ HVAC systems away from fossil fuel-burning systems to electric heat pumps. People are also increasingly adding electric devices like car chargers. In some cases, additions of electric devices will necessitate an upgrade in electric current capability, to 200 or even 400 amps for some large homes and rentals.
“The problem we are having with upgrading homes services has been getting some supplies, especially meter banks,” explains electrician Phil Arsenault, owner of Arsenault Electric in Worcester, and an owner of two triple-decker rentals. Meter banks are installations of multiple meters, to monitor a series of electric services, such as at an apartment complex. “These meter banks have a one-year wait time for delivery. Ever since the start of the pandemic, we have had this issue.”
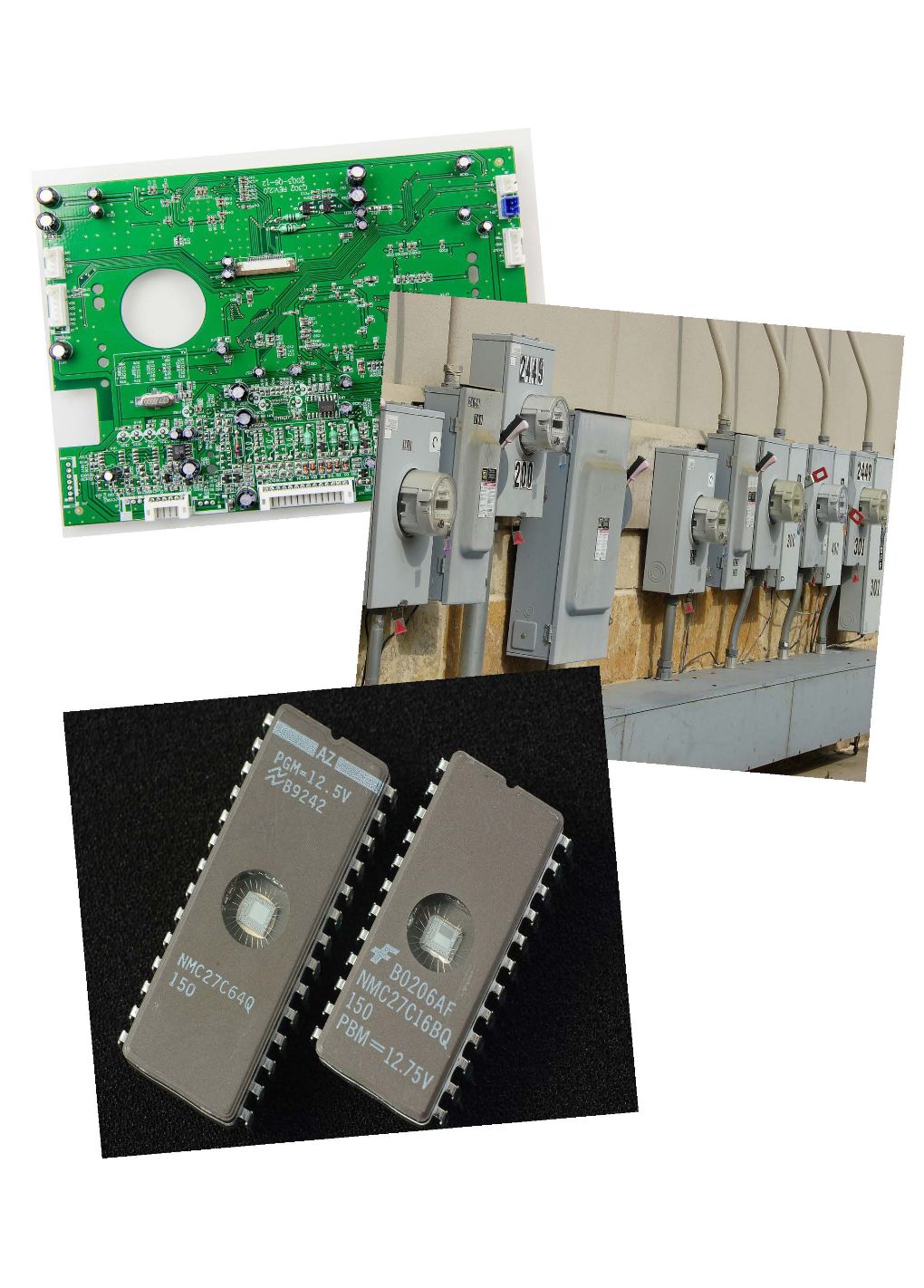
Due to lingering supply chain shortages, electronic components like circuit boards, meters, meter banks and semiconductors remain difficult to obtain, sometimes taking more than a year from the date of order. As a result, service upgrades require planning one year in advance. Image: cc by-sa Wikimedia commons
What Happened to the Supply Chain During the Pandemic?
When the Covid pandemic hit, workplace lockdowns became the norm in many countries around the globe, not least in the United States. China and Hong Kong, the leading manufacturers (along with the U.S.) of electronic parts, instituted some of the strictest lockdowns. As a result of temporary factory and mine shutdowns that lasted through most of 2020 and into 2021, manufacturing suffered a massive setback while orders continued to pour in.
“Demand has always been consistent,” explained Anthony Devlin, service manager at Electrical Experts in Easthampton. “But the drop in availability of parts has put a forward demand on it. We’re just receiving parts now for orders that we placed a year and a half, two years ago.”
Factory and manufacturer lockdowns impacted several tiers of the international supply chain. The shortage of small parts, like circuit boards and transistors, have propagated shortages of components downstream like electric panels, motors and meters. Disruptions in research and design slowed the development of new and updated products. The financial sector was also impacted, further delaying funding needed for new hiring, research and investment in supply chain upgrades.
Further aggravating shortages are the over-consumption of materials. Copper, in particular, has been used beyond its supply. Some manufacturers hoard supplies of copper and other materials in anticipation of changes, further disrupting the supply chain.
Wars and political conflict around the world only exacerbate supply chain problems. In particular, the Russian invasion and ongoing war against Ukraine has diminished essential supplies of metals needed for electronics, as well as grains like wheat and corn. Ukraine was among the world’s top 10 producers of titanium – a metal essential for semiconductor production – and transported iron and steel before the war. The country’s production of metals has dropped off precipitously and is not expected to recover as long as it is under attack. Russia was also a global leader in the production of mined raw materials, including aluminum, nickel and palladium. The country’s depleting war effort and international sanctions have greatly impacted its metals exports. Combined, that war alone has wielded a substantial impact on the electronic parts supply chain.
It hasn’t only been electronic components that have been affected by supply chain disruptions. Nearly all consumer products – cars, houses, food, gas, toilet paper – had depleted inventories in 2020, sending prices skyward. But electronic products, in particular, have continued to struggle to meet demand. A global push to convert home HVACs to electric, alongside a massive addition of electric smart home products and electric cars, have further exacerbated the shortage of supplies.
Once Covid lockdowns lifted and factories began operations again, many found themselves ill-equipped to catch up on back orders. Some were still relying on outdated operation models that didn’t take enough advantage of automation and AI technologies. And most companies haven’t been able to hire and onboard workers fast enough to sufficiently catch up with increasing demand.
The pandemic disruption to the global supply chain has been so broad that it continues to lag behind demand four years later. While some household products have bounced back somewhat, many electronic components continue to be back ordered for a year or more.
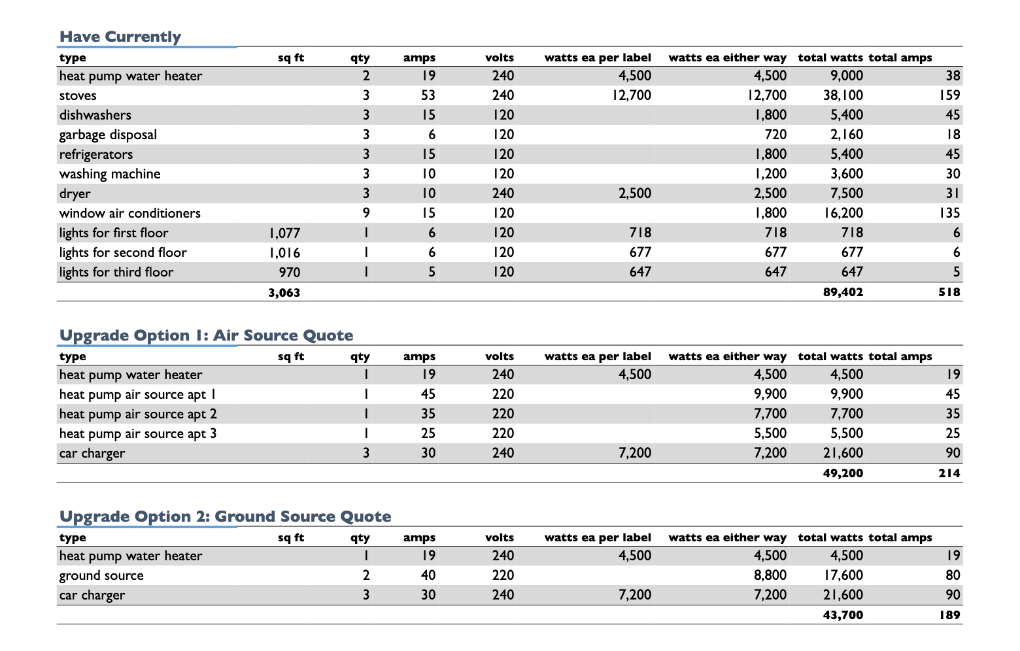
This sample electric load calculation for a three-decker in Worcester shows watts usage of various electric appliances, indicating a need for increased amperage. Although the table was generated by a non-electrician using best available appliance labels or other data, and may have individual wrong numbers, the message is clear: Moving to heat pumps requires 50% more amperage. Since many buildings are already under-amped and rely on timing to ensure breakers don't pop, a service upgrade will be required. Image: MassLandlords
Planning Ahead
For landlords and other electric service customers, the electronic parts backup necessitates some wise forward planning. Some equipment failures are unpredictable, such as when outside components like heat pumps are damaged during storms and need replacing.
“We try to be up front with our customers,” said Devlin, “we try to explain that service orders are on a wait list. Whatever inventory we have is still going to back orders.”
Other electric service projects can be planned ahead. Installation of heat pumps and high voltage car chargers, in many cases, will require an upgrade to electric current. That means new outside wiring, piping and meters, as well as indoor (or outdoor, depending on where panels are affixed) electric panels and breakers.
“The longest wait time I’ve seen is for utility meter sockets,” said Devlin. A meter socket is the outdoor junction at which the utility’s incoming electric power first comes in contact with your home system. “Meter sockets have changed for new regulations, and demand for them is so high that getting them is not easy. And the price on those sockets is nearly three times what it was before Covid.”
For amperage upgrades, plan at least a year ahead.
From 30 Amp to 400 Amp
Electric needs have continuously expanded since home electricity became available in the 1920s. Home electricity was a luxury through the 1920s and 30s. But with support from President Franklin Roosevelt’s Rural Electrification Act of 1936, home electricity became the standard in the U.S. by 1945. By 1960, nearly every home had electricity.
For many of those years, electricity was used only to provide lighting, and maybe power a furnace for heating. A 30-amp electric panel was sufficient for a home until about 1950. Then an onslaught of electric appliances hit the market in the mid-20th century. Refrigerators, TVs, then water heaters, washing machines, ovens, clothes dryers, toasters, air conditioners, baseboard and space heaters and dishwashers became must-have residential items. By 1970, 100-amp panels became the norm.
Amps (or amperes) are a measure of electric current. The higher a system’s amperage, the more wattage of electricity is able to flow through the circuits. More electric need necessitates higher wattage, and more electric current capability. Devices like high-voltage car chargers draw a relatively high amount of electricity compared to other home devices.
Inventions of new electric appliances has not slowed. Home offices with computers, printers and other accessories have increased in popularity since 2020. Electric heat pumps and car chargers are becoming commonplace. “If your average home has 100 amp and you want a car charger, I can almost guarantee you’ll need 200 amp,” said Devlin. “For new homes, 200 amp is now the standard.”
It has long been the standard for multifamilies. “The typical multifamily house has a 200-amp service,” said Arsenault. “A three-family house is capable of carrying 200 amps combining all loads. The panel for each apartment is typically 100 amp.” When you run a stove, clothes dryer and water heater all at the same time along with kitchen and bath usage, “you could potentially exceed the 100 amps,” said Arsenault. Adding a car charger or heat pump to that load would likely require upgrading to 400-amp service, with 200 amps per rental unit.
Devlin is noticing 400-amp orders increasing as well. “400 amp is starting to pop up more and more. It’s starting to become more common.” The day may be coming when 400-amp service is the new standard, Devlin said. This will be especially true for homes with luxury items like hot tubs, swimming pools and heated garages.
Supply Chain Improvements?
There may be better news in the near future regarding the electronic parts supply chain. Demand has slightly diminished for a few parts in 2023 and some forecasts predict a trend. Orders for computer chips fell 9% in October 2023, according to EMS Now, a trade publication of the electronics manufacturing services industry. And the S&P Global PMI (Purchasing Managers Index) for electronics equipment orders showed a decline over the past year.
These metrics suggest a relative slowdown in demand that may continue. Wait times for parts would presumably follow. Still, in this age of mass electrification and transition away from fossil fuels, electronic components will remain in high demand. It’s possible the pre-Covid wait times of 8-12 weeks is a relic of history. New wars abroad and political strife never improve the outlook.
All of which means, as property owners, our capital planning may need big adjustments. Your list of vendors might need expanding, to give more options when emergency repairs or replacements are needed. Major projects, like electric panel upgrades and car charger installations, must be planned a year in advance. Purchases of large components like heat pumps and electric meters will require more research to determine best pricing.
You can also make changes to daily activities, and coach your tenants to do so, in order to lower electricity usage loads. If you use a car charger, plug in only at night, when other electricity use is low. And while it may not work, you could suggest to your tenants that they could avoid doing laundry, especially running the clothes dryer, on weekends and holidays when everyone else is doing it. Better yet, provide your tenants with clotheslines and racks to hang up their wet laundry, when practical, and skip the clothes dryer altogether. Set the dishwasher to run late at night, after lights and electronics are turned off. Give tenants power strips for devices like computers, TVs and game consoles and show them how to turn off the power strip when not in use, to avoid wasteful low-level electric draw.
The all-electric home or rental, devoid of fuel-burning devices, is more efficient and environmentally friendly. Converting dwellings to electricity is our best hope for mitigating disastrous warming of the atmosphere, and will be cheaper in the long run. For the time being, however, this period of mass electrification is causing a bottle neck of supply for parts and materials that we may have to adjust to and work around.
We invite you to share your electric upgrade experiences with us. If you’ve had better success in obtaining parts and getting service repairs or upgrades than what statistics and electricians describe, please let us know by commenting below or sending email to hello@masslandlords.net.